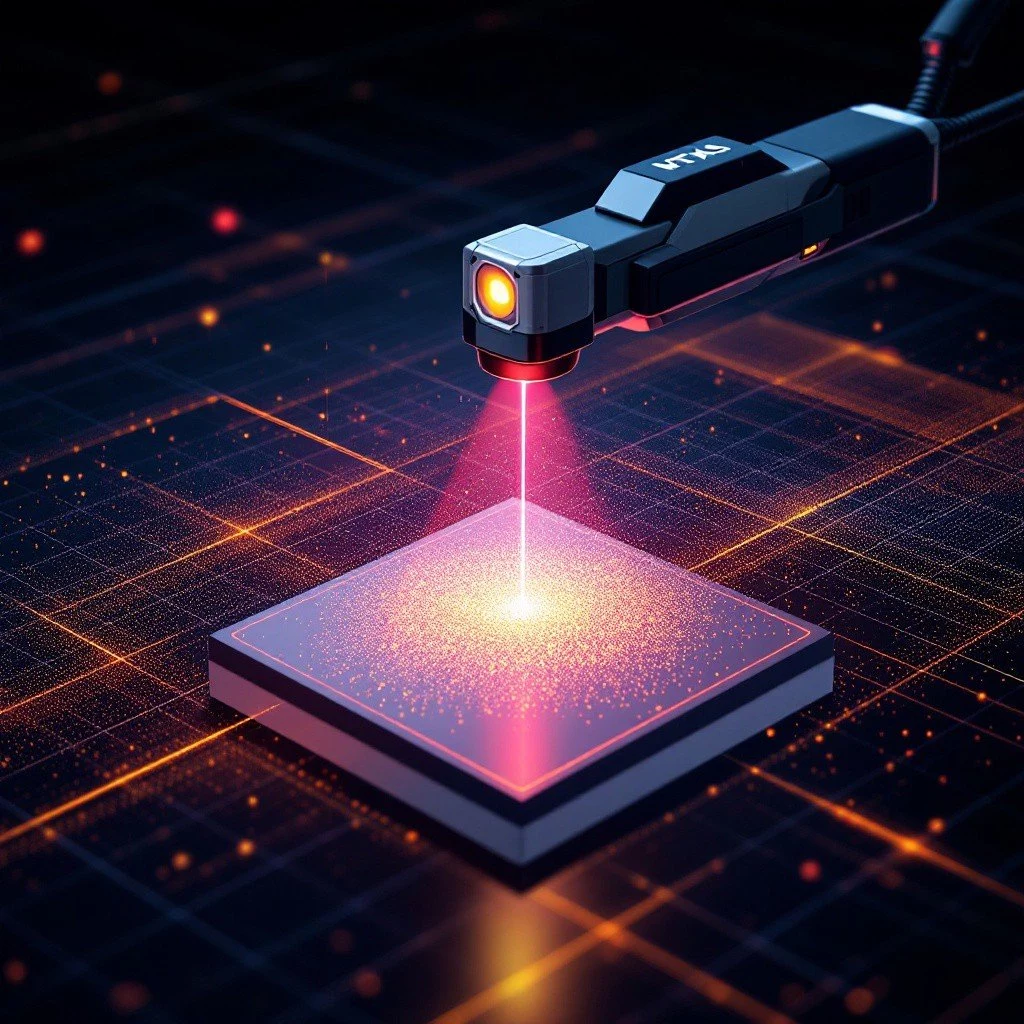
What is Laser Scanning, and How Does It Work in Generating Point-Cloud Data?
Laser scanning is a transformative technology that has revolutionized how we capture spatial data for various industries, including architecture, engineering, construction, manufacturing, and forensics. This advanced process involves using laser beams to collect highly accurate measurements, ultimately creating a digital representation of physical objects or environments in the form of point-cloud data.
In this comprehensive article, we’ll delve deep into the mechanics of laser scanning, explore how it generates point-cloud data, and understand its applications, benefits, and challenges. This detailed overview will not only explain the technology but also help you appreciate its critical role in shaping modern industries.
What is Laser Scanning?
Laser scanning, also known as LiDAR (Light Detection and Ranging) or 3D laser scanning, is a non-contact technology used to measure distances and capture spatial data. It relies on laser beams to scan an object or environment and record precise 3D coordinates of its surfaces. These coordinates form a dense set of data points known as a point cloud.
Point-cloud data represents the geometry of a scanned object or space in fine detail, often enriched with information like color, intensity, or reflectivity. This data is essential for creating 3D models, simulations, and analyses in a wide range of applications.
How Does Laser Scanning Work?
The process of laser scanning involves sophisticated hardware and software working together to capture spatial data accurately. Here’s a step-by-step explanation:
1. Laser Beam Emission
A laser scanner emits a focused beam of light (laser) toward the surface of the target object or environment. The scanner's system directs this beam in a controlled pattern, covering the area of interest systematically.
2. Reflection of Laser Beam
When the laser hits a surface, it reflects back to the scanner. The intensity and duration of the reflection provide key information about the distance and properties of the surface.
3. Distance Measurement
The scanner calculates the distance between itself and the surface using one of two primary methods:
- Time-of-Flight (ToF): Measures the time it takes for the laser to travel to the surface and back. The formula d=ct2d = \frac{ct}{2}d=2ct is used, where ccc is the speed of light and ttt is the round-trip time.
- Phase-Shift Measurement: Analyzes the phase difference between the emitted and reflected laser waves, providing higher accuracy over shorter distances.
4. Angular Positioning
As the scanner emits laser beams, it also records the horizontal and vertical angles at which the beam was directed. This angular data helps determine the exact location of each reflection point in a 3D space.
5. Generating a Point Cloud
Each reflected laser beam represents a point in a 3D coordinate system. By emitting millions of laser pulses per second, the scanner captures a vast number of data points, collectively forming a point cloud. This point cloud is a digital replica of the scanned object or space.
6. Data Processing
Point-cloud data is processed using specialized software to clean, align, and organize the points. Advanced algorithms may be applied to filter out noise, fill gaps, and generate precise 3D models.
Components of a Laser Scanning System
A laser scanning system consists of several key components that work together to capture and process spatial data effectively:
- Laser Source: Emits laser beams for measurement.
- Receiver/Detector: Captures the reflected laser signal to calculate distance and intensity.
- Rotating Mirror or Mechanism: Directs the laser beams across the target area, ensuring comprehensive coverage.
- Positioning System: Tracks the scanner's orientation and position using GPS, inertial navigation systems (INS), or external references.
- Processing Unit: Processes raw data into point clouds or models.
- Software: Used for analyzing, cleaning, and converting point clouds into actionable outputs like 3D models or CAD files.
Applications of Laser Scanning and Point-Cloud Data
Laser scanning has become indispensable across industries due to its precision and versatility. Below are some of the most prominent applications:
1. Architecture, Engineering, and Construction (AEC)
- Capturing existing conditions for renovations and retrofits.
- Generating accurate 3D models for Building Information Modeling (BIM).
- Performing clash detection in complex construction projects.
2. Topographic and Land Mapping
- Creating detailed terrain maps for infrastructure projects.
- Supporting environmental monitoring and natural disaster management.
- Assisting urban planning with accurate city models.
3. Manufacturing and Quality Control
- Inspecting components for dimensional accuracy and defects.
- Creating digital twins of machinery and equipment.
- Reverse-engineering parts for redesign or replication.
4. Cultural Heritage Preservation
- Digitally preserving historical monuments, artifacts, and sites.
- Documenting intricate details that may be lost over time.
5. Forensics and Law Enforcement
- Reconstructing accident scenes or crime sites for analysis and evidence presentation.
- Providing visual data for court cases and investigations.
6. Entertainment and Virtual Reality
- Capturing real-world environments for immersive VR experiences.
- Creating realistic 3D assets for video games and films.
Advantages of Laser Scanning
Laser scanning offers numerous benefits compared to traditional surveying and measurement methods:
1. High Precision
Captures measurements down to millimeter-level accuracy, essential for detailed projects.
2. Time Efficiency
Can scan large areas in minutes or hours, compared to days or weeks with manual methods.
3. Comprehensive Data
Provides complete 3D spatial information, reducing the need for revisits and ensuring all details are captured.
4. Non-Invasive Measurement
Works without physical contact, preserving fragile or hazardous objects and environments.
5. Cost Savings
Reduces expenses related to material waste, prototyping, and rework by identifying issues early.
Challenges and Limitations
While laser scanning is a powerful technology, it does come with certain challenges:
1. Cost
High-quality laser scanners and processing software can be expensive, posing a barrier for smaller organizations.
2. Data Volume
Point clouds are large datasets requiring significant storage and computing power to process.
3. Environmental Interference
Factors like fog, dust, rain, or reflective surfaces can affect the accuracy and quality of the scanned data.
4. Skill Requirement
Interpreting point-cloud data and using advanced software requires specialized training and expertise.
Future of Laser Scanning
As technology advances, laser scanning is becoming faster, more affordable, and more accessible. Innovations in LiDAR, AI-driven data processing, and integration with other technologies like drones and augmented reality are further enhancing its capabilities. These advancements are expanding the scope of laser scanning into new fields, such as autonomous vehicles and smart cities.
Conclusion
Laser scanning has transformed how we measure, document, and analyze physical spaces, offering unmatched precision, efficiency, and versatility. By generating detailed point-cloud data, it enables industries to make informed decisions, improve workflows, and achieve superior results. As this technology continues to evolve, its impact on design, construction, manufacturing, and beyond will only grow.